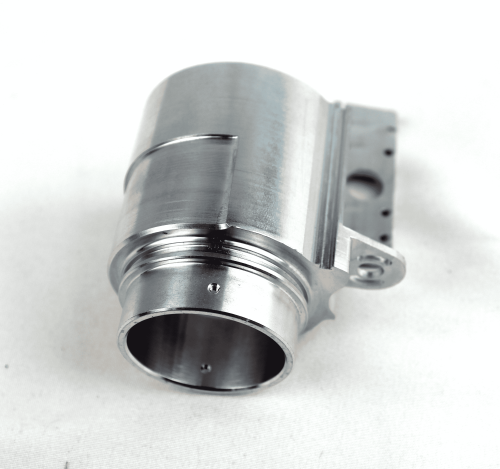
Aluminum milling parts are components created by machining aluminum using a computer numerically controlled (CNC) milling machine. Aluminum is a popular material for CNC machining due to several advantages:
Strength-to-weight ratio: Aluminum is lightweight yet relatively strong, making it ideal for applications where weight reduction is a priority, such as aerospace and automotive parts.
Machinability: Aluminum is considered a soft metal compared to other metals commonly used in CNC machining, like steel. This translates to easier machining, reducing production time and cost.
Corrosion resistance: Aluminum naturally forms a thin oxide layer that protects it from corrosion. Additionally, various surface treatments can further enhance its corrosion resistance.
Thermal conductivity: Aluminum conducts heat well, making it suitable for heat sinks and other thermal management applications.
Electrical conductivity: While not as conductive as copper, aluminum offers good electrical conductivity, making it useful for electrical components.
** recyclability:** Aluminum is highly recyclable, making it an environmentally friendly choice.
Here are some of the details to consider when using aluminum for milled parts:
Aluminum alloys: Different aluminum alloys offer varying properties in terms of strength, machinability, corrosion resistance, and weight. Common alloys used for CNC machining include 6061, 7075, and 2024.
Design for manufacturability (DFM): When designing aluminum parts for milling, its crucial to consider factors like minimum wall thickness, corner radii, and draft angles to ensure efficient and cost-effective machining.
Tolerance and surface finish: CNC milling can achieve tight tolerances for aluminum parts. The desired surface finish will also influence the machining process and cost.